HOW DO I STOP MY FAST-ACTION DOORS FROM BEING DAMAGED?
0 min read
Many factories use high speed doors to improve environmental control through high use doorways. These doors are on a timer so they close automatically after a few seconds. Whilst being a great way to save energy and increase productivity and safety, high speed doors can also be susceptible to being damaged – especially by forklift trucks!
So how can you stop your high-speed doors from being damaged by forklift trucks? The easy answer is train your forklift drivers better, however not only is that a bit tongue-in-cheek, it’s also not always the problem.
So here’s 7 ideas from Tekta on how you can prevent damage to your rapid
action doors.
ANTI-CRASH & SELF-REPAIRING SPEED DOORS
There are various speed doors on the market which aim to minimize damage to the door if it is hit, here are the most popular types.
Zipper-edge speed door
This type of speed door has a beading (zipper) system on the edge of the PVC curtain which is used to retain the curtain in the side guides. One major benefit of this type of door is that there are no wind bars within the curtain, this means that even if the curtain is hit higher up than the bottom bar then there is nothing to bend. The bottom edge of these doors will be a soft pocket, sometimes weighted depending on the manufacturer and model. One potential issue with these doors is they may not always perform well on large, external openings especially in high winds due to friction build up in the guides so be sure to discuss this with your supplier. For example of this type of door look at our Rapidor Impact speed door.
Anti-crash bottom bar
In this type of door, the main part of the door curtain will be secured with wind bars as a traditional speed door, however the bottom bar will have a system allowing it to crash out if there is an impact without damage. Some manufacturers use a flexible bottom bar, others use special tabs on the ends of the bar. One disadvantage of this type of system is that it often cannot be used on windy openings as the door will blow out. Our Rapidor Pro speed door is one type of door which offers this option.
Sacrificial break-out system
This is a variation of the anti-crash bottom bar where the side tabs are designed to break and be easily replaced if there is an impact. The beauty of this design is in its simplicity, however purchasing the new tabs can be expensive from some manufacturers and also you will have to spend time making the repair.

USE AUDIO-VISUAL WARNING SYSTEMS
It is worth considering how you can make your drivers life easier, for example using audio-visual warning systems to help prevent forklifts from crashing into your speed doors. Here are a few options:
Traffic lights
Use an LED traffic light to signal red until the door is fully open. By ensuring this is in clear line of site for the driver you can greatly reduce the risk of an impact. Variations of this include flashing warning strips around the door itself and also flashing beacons which flash whilst the door is moving in either direction.
Sounders
Beware as this may cause headaches! However you can also use a sounder that makes a noise whilst the door is in motion.

BI-PARTING DOORS ALLOW FASTER OPENING AND BETTER VISION
Bi-parting (side-opening) speed doors are a lesser known option in the UK market. However they can offer a very effective solution to reduce the chance of impact damage for sites with busy doorways:
Faster speeds
Bi-parting doors are usually faster than roll up doors for two reasons. The first is that because the door is moving apart from the middle rather than up from the bottom the opening speed is effectively double. Secondly, many forklift access doors are narrower than they are tall so this means that the door opens quicker as there is less distance to travel.
Better vision
one of the common causes of damage to rolling doors is that forklift drivers do not have good vision of the door as it is opening, they need to crane their necks to see if the door has cleared their mast. With a bi-parting door the driver has a clear line of site as the door opens directly in front of them and they can see clearly if the opening is wide enough for their vehicle.
An example of a bi-parting speed door is the Rapidor Sprint.

REVIEW THE AUTOMATION OF YOUR DOORS
This should really be point 1 on the list because it’s where we would recommend you always start and you can refer to our Activation Guide for even more information. Ask – how are the doors being used and are we making it as safe, easy and simple as possible for the operators to help them avoid crashing into the rapid doors? Here are a few common issues:
Remote controls, using remote control fobs to operate speed doors is a very popular option. However it can present issues, for example if the buttons on the fob are small the operator might not click the button fully and therefore may crash into the door. Additionally remote control fobs are dependent on the operators timing and they may simply leave it too late! One potential solution here might be to use a remote push button fixed to the forklift which makes it easier for the operator. We would also recommend considering a TOF spot laser sensor instead of a remote control as this means you can decide and fix the activation point and range.
Pull cords are another common activation method but they can be problematic both from an activation and a safety point of view as the operator has to stretch to grab the cord. Our recommended solution here is to use TOF spot laser sensors.
Induction loops are a very popular and reliable method of activating rapid doors, the common issue here is if the loops are incorrectly positioned. For example if they are too close the door then it might not have time to fully open. If they are too far away then the door may be activated inadvertently by other traffic and the door could have started closing again from a previous cycle, confusing the drivers. Your door installer should be able to work with you to identify the correct positioning for the floor loops. The same problems and solutions also apply to radar or motion sensors which are commonly positioned above the doorway.
Another thing to consider which may not be so obvious is whether to set the activation so that forklifts have to STOP! Usually in search of maximum productivity activation will be set up to try and ensure the door is open by the time the vehicle reaches it, however maybe it’s worth a few “wasted” seconds on each activation in order to reduce your repair bill on broken doors dramatically!?
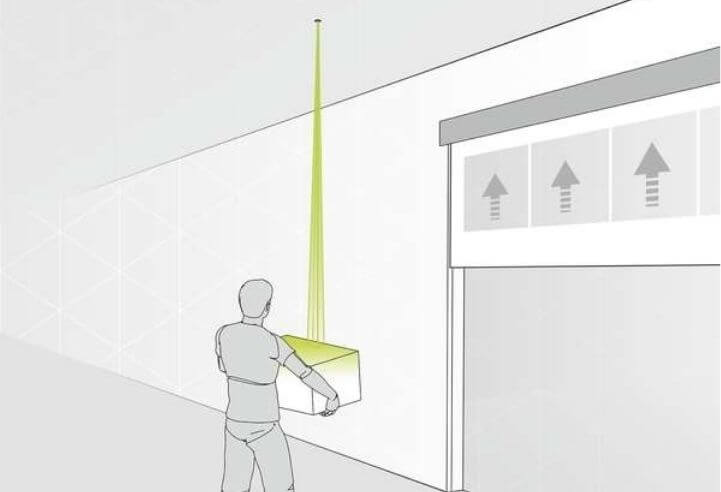
USE LIGHT CURTAINS RATHER THAN SAFETY EDGES
In order to comply with safety regulations all doors which close automatically require a safety system to ensure they can’t close on persons or objects. The traditional way of achieving this has been with a safety bottom edge which causes the door to go back up when it strikes something. Usually there will be a back up photocell at low level which will pick up anything protruding into the doorway at this specific point (usually around 300mm from the ground). The problem with safety edges is that depending on the speed and direction of the forklift, the damage may have already been done by the time the door retracts if there is a crash.
It is highly recommended to use safety light curtains instead of the safety edge/photocell combination – this provides a continuous grid of light through the doorway picking up any objects as soon as they protrude into the opening. This can be further enhanced with the use of presence or motion sensors which allow objects to be picked up when they are further away from the door, helping to reduce the risk of impact damage from forklifts.

INSTALL PROTECTION AROUND THE DOORS
The rest of the suggestions above refer to the risk of hitting the door curtain when it is partly open or partly closed. However another common issue is the doors surrounds such as the side guides and the head roll and cover getting hit by forklifts.
There are many ways to help prevent this. At the basic end of the scale you could look at painting simple and cheap floor hatchings and line markings to clearly signify the roadway to the driver. You could use bollards to protect the side guides at low level, or railings or guardrails to prevent the vehicle from veering off the roadway. The full-scale solution is a complete goalpost protector frame which protects all three sides of the door from impact damage.

FASTER DOORS…
Some “speed” doors on the market are simply too slow for the job they are being asked to do. When purchasing a new speed door be careful you understand how long the door will take to open and to close. For example if a maximum opening speed is quoted, this will refer to the maximum speed the door reaches, however many doors have a soft-start and soft-stop feature so this will slow down the overall speed. Usually issues with speed can be overcome with some of the other suggestions in this list, however in some cases it might be worth considering replacing the door with a faster solution.

In conclusion there’s many ways you can consider to prevent frequent and expensive repair bills due to impact damage to your high speed doors. We trust this guide has been helpful, however it is not exhaustive so please let us know if we’ve missed something or if you’ve come up with your own unique idea.
Our Complete Guide to High Speed Doors gives a great overview of when & where to use the many different types of high speed door that are available