Industrial door servicing: how do I know it’s being done properly?
0 min read
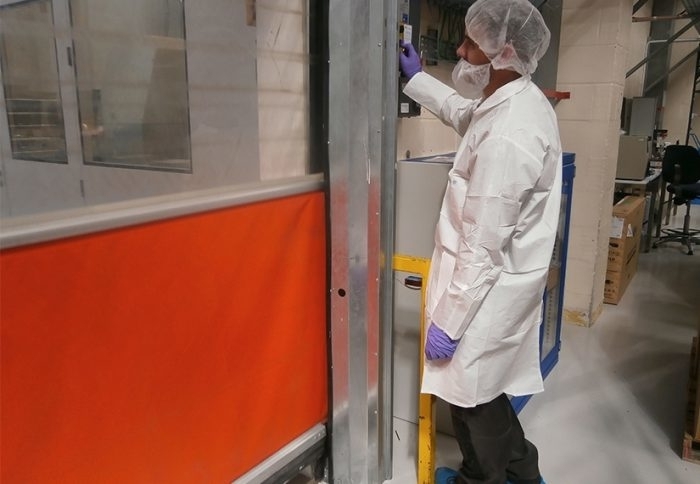
This is a question we are often asked because industrial door servicing and contract pricing aren’t generally fixed. There is no rigid set of procedures for the contractors who are conducting your industrial door repair; however, there is a difference between a service which will include actual improvements, and a survey which will merely identify them. If your assets are not serviced properly then this could reduce their lifespan by up to 50%. This guide is designed to help you understand what you should expect during an industrial door and dock leveller servicing appointment. To arrange your next review, get in touch with the team today.
Five things to consider before an industrial door repair or service
Time spent on site
The time spent servicing each industrial door can vary from 10 minutes to 1 hour from one contractor to the next. There’s no correct amount of time because it depends on the condition of the door. However, if your contractor is spending less than 20 minutes per asset then you can be fairly sure that they’re not doing a thorough job. If you’re looking to move to a new contractor then it’s a good idea to give them an idea of how many hours your existing contractor spends on site (i.e. two engineers for one day would be approximately 16 hours) so that they can give you an accurate industrial door servicing quote.
Certification
You should be provided with a detailed certificate following each industrial door repair or maintenance visit explaining whether each asset, from your dock leveller to the door itself, is compliant, requires improvement, or is non-compliant. This should be followed with a remedials’ quotation for the assets which require improvement or are non-compliant.
Lubrication of moving parts
Your contractor should lubricate all moving parts on the assets that they service. If this is not part of your service contract then it will lead to the quicker deterioration of these parts and your industrial door may need to be replaced sooner than expected.
Replacement of minor parts
Part of your service contract should include the replacement of worn parts on industrial doors and dock levellers such as brush seals and sectional door rollers. The cost for this should be built into the contract as it will save the travel cost of the engineer coming back to the site to carry out these works.
Additional services
There are two additional services that some contractors offer which may be of interest:
• Force testing
If you have doors with a safety edge then your contractor should carry out force testing under the latest DHF regulations. This is to detect the amount of downward force exerted by a closing door before the safety edge detects an obstruction, stops and sends the door back up. If the force is over a certain level then your industrial doors will not be compliant.
• Cleaning
Some dock leveller servicing packages include a thorough cleaning of your dock leveller pits. This is an essential part of your dock leveller maintenance since without it, it will be very difficult to detect oil leaks in future. The cleaning of other assets such as sectional doors is an additional service that can be offered if required.
To arrange your next industrial door servicing, get in touch with Tekta today.